How Can You Manage Office Supply Inventory Effectively?
In the quest to streamline office supply management without succumbing to the pitfalls of overstocking, we've gathered insights starting with a Professional Development Consultant's strategy to 'Conduct a Lean Inventory Audit'. Alongside expert advice, we've compiled additional answers including practical tips from various office professionals. These range from leveraging technology with barcode systems to setting smart re-order thresholds, ensuring efficiency in every paper clip and pen.
- Conduct a Lean Inventory Audit
- Implement Barcode Tracking System
- Outsource to Inventory Specialists
- Adopt Just-In-Time Stocking
- Utilize Digital Order Platforms
- Establish Re-Order Thresholds
Conduct a Lean Inventory Audit
As a former Office Manager for Fairlife, conducting a lean inventory audit was very effective. It involved mapping out all current supplies and usage rates, then categorizing items based on necessity and frequency of use. By applying lean principles, you can eliminate excess and streamline ordering processes. For example, categorizing supplies into A, B, and C groups (where A items are high-use, essential supplies, and C items are low-use, non-essential supplies) helps prioritize ordering and reduces overstocking.
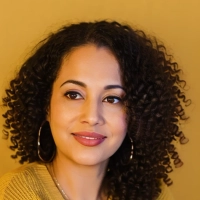
Implement Barcode Tracking System
Integrating a barcode tracking system for managing office supplies can significantly streamline the inventory process. By scanning items as they are used, you can automatically update stock levels and track usage patterns. This real-time data allows for accurate forecasting, preventing overstocking or running out of critical items.
It also simplifies the process of restocking, as you know exactly what needs to be ordered and when. If you haven't already, consider setting up a barcode tracking system to maintain an efficient office supply chain.
Outsource to Inventory Specialists
Outsourcing inventory management to specialists can be a strategic move for a business aiming to focus on its core competencies. The experts come equipped with the knowledge and tools to maintain supply levels effectively, often bringing in advanced techniques and software for monitoring stock. This can lead to cost savings through bulk purchasing and a reduction in the time staff spend managing supplies.
Specialists can also provide insights into usage trends and suggest improvements to purchasing strategies. Explore the option of hiring a third-party inventory management team to optimize your office supply process.
Adopt Just-In-Time Stocking
Adopting a just-in-time stocking approach can significantly reduce waste and costs associated with excess inventory. This method involves ordering supplies only as they are needed, reducing the space required for storage and minimizing the risk of items becoming obsolete. To implement this strategy, closely monitor supply levels and demand to ensure timely reordering.
Effective communication with suppliers to ensure quick turnaround times for orders is also critical. Begin reviewing your current inventory system to see if a just-in-time approach could work for your office needs.
Utilize Digital Order Platforms
Utilizing digital supply order platforms can enhance the efficiency of managing office supplies. These platforms often feature tools that can automate reordering processes, track spending, and provide analytics on supply usage. By digitizing these tasks, you can reduce the likelihood of human error and free up time for employees to focus on more valuable work.
Additionally, some platforms allow for integration with other business systems, creating a seamless workflow. If you're looking to improve your supply management, investigate digital platforms that could fit into your existing operations.
Establish Re-Order Thresholds
Establishing re-order thresholds for each item in your office supplies can prevent the inconvenience of running out and the expense of urgent orders. By determining the minimum stock level that triggers a reorder, you ensure that there is always a buffer of supplies on hand. This method requires initial analysis to determine appropriate levels for different items, but once in place, it helps maintain a consistent stock without over-ordering.
It also enables budget planning and can reduce shipping costs by combining orders for multiple items when they hit their thresholds. Take the first step by analyzing your current supply usage and set re-order points to automate your inventory management.